La produzione di un impianto di produzione è un ambiente complesso con una moltitudine di risorse fisiche da misurare e gestire, che vanno da grandi azionamenti e macchinari a componenti più piccoli come sensori e batterie. La maggior parte delle strutture dispone di un programma di manutenzione preventiva per tali apparecchiature, soggette ad usura, basato su misurazioni specifiche. Ma che dire dell’infrastruttura di rete? Come si può valutare questa importante struttura?
Le reti Ethernet in ambito manifatturiero si sono sviluppate in un’importante interfaccia tra i sistemi di produzione e di automazione e i sistemi aziendali e rappresentano il percorso di comunicazione standard tra i sistemi di automazione. La crescita e la standardizzazione della tecnologia Ethernet all’interno dei sistemi automatizzati è accompagnata da due importanti requisiti: In primo luogo, la necessità di rendere il personale di controllo e di produzione consapevole di quali dispositivi sono collegati alla rete Ethernet in ogni sede e, in secondo luogo, le prestazioni di questi dispositivi.
Il monitoraggio e la misurazione delle prestazioni dei dispositivi è importante per gestire correttamente l’integrità complessiva della rete di produzione. Questo white paper esamina tre best practice per la determinazione delle metriche per garantire che l’intera rete industriale di gestione e di operazioni possa essere gestita in modo efficace ed efficiente.
Primo passo: comprendere l'importanza degli indicatori di performance
Il primo passo per gestire adeguatamente la rete produttiva consiste nel determinare i fattori da misurare e poi consolidare la lista per individuare gli elementi più rilevanti per gli obiettivi organizzativi e l’integrità dei sistemi. Queste metriche chiave sono note come Key Performance Indicators (KPI). Un KPI è una metrica conteggiabile che viene utilizzata da un’organizzazione per determinare la misura in cui gli obiettivi operativi e strategici vengono raggiunti. I KPI sono unici per l’organizzazione e si basano sulle prestazioni di ogni reparto che ci si aspetta garantisca il successo complessivo dell’organizzazione. Diverse metriche combinate possono formare un unico KPI.
Le caratteristiche di base necessarie per l’introduzione di un KPI efficace son:
- Facilità di comprensione
- Monitoraggio
- Valore reale
- Numero ridotto
Fonte: „The Choice of KPIs in BSC implementation.“ Business Analysis Toolkit. 2008-2015 https://www.measurebusiness.com/the-choice-of-kpis-in-bsc-implementation.htm
Secondo passo: definire gli indicatori chiave di performance
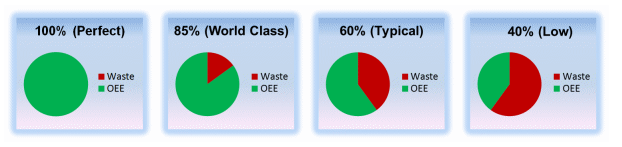
Figura 1: Riconoscere l’importanza del valore GAE di un’azienda per ottenere miglioramenti e identificare i problemi nell’area di produzione.
Fonte: OEE (Overall Equipment Effectiveness). Vorne Industries, Inc. 2011-2016. https://www.leanproduction.com/oee.html
Come risultato dell’emergente utilizzo della tecnologia Ethernet nell’industria e del conseguente passaggio da sistemi stand-alone ad apparecchiature in rete, i produttori di livello mondiale hanno capito che devono considerare il tempo produttivo dell’infrastruttura di rete industriale come un importante fattore di GAE. Sulla base di questa realizzazione il management di queste aziende sta cercando il modo di cambiare i loro processi operativi.
Ad esempio, molte aziende adottano procedure di risoluzione dei problemi per la loro infrastruttura di rete di produzione, quindi se la rete non è disponibile, il problema deve essere risolto immediatamente per rimettere in funzione l’impianto. Questo è il risultato diretto dell’elaborazione dei dati KPI per un segmento di impianto (ad esempio una macchina o una cella), che non riflette necessariamente la natura di rete delle operazioni industriali odierne.
Si tratta di un approccio cruciale per le aziende in cui i problemi nella rete industriale influenzano la produzione. Invece di cercare un’interruzione in una cella o in una macchina quando gli effetti sono chiari ma la causa originale è oscura, un approccio più efficace potrebbe essere quello di indagare le prestazioni dell’intera infrastruttura di rete industriale e le sue interazioni con le varie macchine dell’impianto.
Per definire un KPI che aiuti un’organizzazione a raggiungere un tempo di produttività di rete quasi ideale al 100%, è necessario innanzitutto decidere quali dispositivi all’interno della rete industriale devono funzionare 24 ore su 24, come le interfacce uomo-macchina (HMI), i controllori a logica programmabile (PLC), i controllori di ingresso/uscita (I/O), gli interruttori industriali e gli azionamenti che causerebbero il blocco della produzione se fossero difettosi.
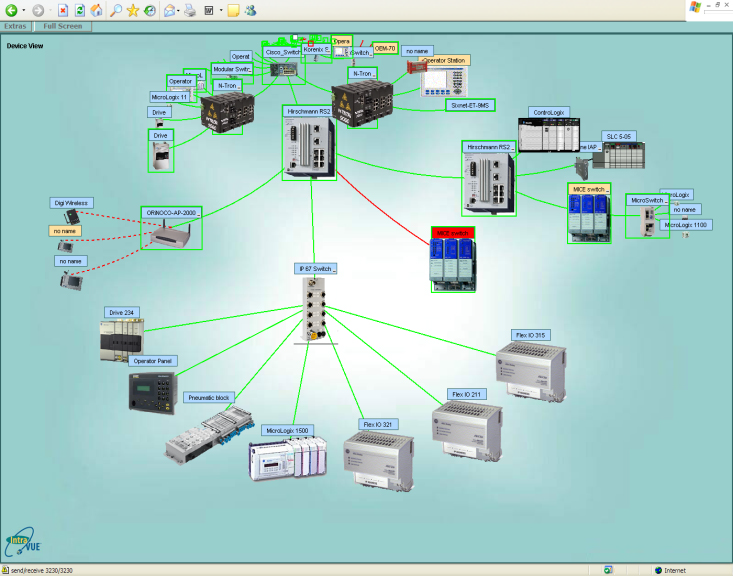
Figura 2: Questo diagramma mostra i numerosi dispositivi e punti di connessione che possono far parte di una rete industriale..
Terzo passo: prendere decisioni informate sulla base dei rapporti sui dati KPI
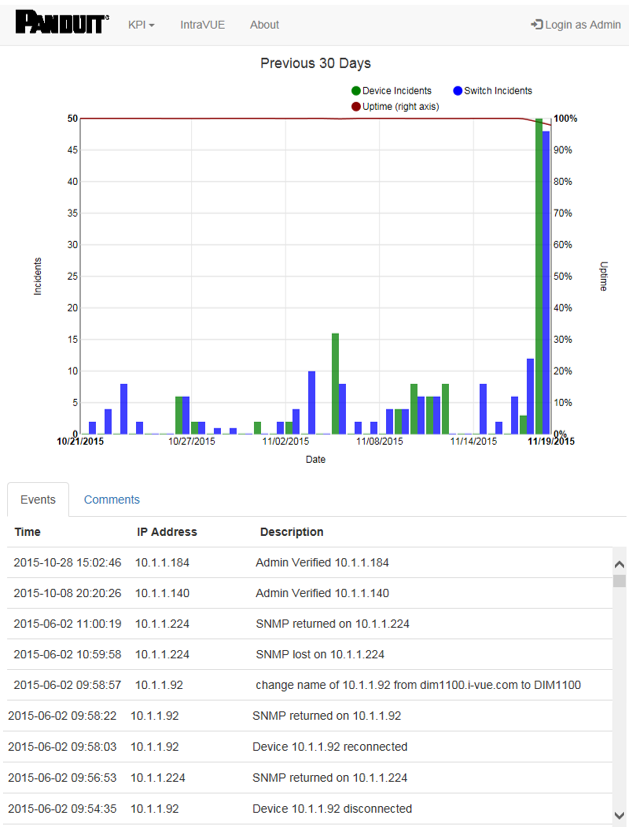