Die Fertigung eines Produktionsbetriebs ist ein komplexes Umfeld mit einer Vielzahl von zu messenden und zu verwaltenden physikalischen Ressourcen, die von großen Antrieben und Motoren bis hin zu kleineren Bauteilen wie Sensoren und Akkus reichen. In den meisten Anlagen gibt es für solch verschleißanfällige Objekte zwar ein vorbeugendes Wartungsprogramm, das auf bestimmten Messungen basiert, aber wie steht es um das Fertigungsnetzwerk? Wie kann diese wichtige Anlage bewertet werden?
Ethernet-Netzwerke für die Fertigung haben sich zu einer wichtigen Schnittstelle zwischen Produktions- und Automatisierungssystemen und Business Systemen entwickelt und stellen den Standardkommunikationspfad zwischen Automatisierungssystemen dar. Das Wachstum und die Standardisierung von Ethernet innerhalb automatisierter Anlagen wird von zwei wichtigen Anforderungen begleitet: Erstens, der Notwendigkeit, Kontroll- und Produktionsmitarbeitern bewusst zu machen, welche Geräte an jedem Standort an das Ethernet-Netzwerk angeschlossen sind, und zweitens, welche Leistung diese Geräte erbringen. Die Überwachung und Messung der Geräteleistung ist wichtig, damit die Gesamtintegrität des Fertigungsnetzwerks ordnungsgemäß verwaltet werden kann. In diesem White Paper werden drei bewährte Methoden zur Bestimmung von Messgrößen untersucht, damit das gesamte Industrienetzwerk von Management und Betrieb effektiv und effizient betrieben werden kann.
Erster Schritt: Die Bedeutung von Leistungskennzahlen verstehen
Der erste Schritt zur angemessenen Verwaltung des Fertigungsnetzwerks umfasst die Bestimmung der zu messenden Faktoren und daran anschließend die Konsolidierung der Liste, um die für die organisatorischen Ziele und die Integrität der Systeme wichtigsten Elemente zu identifizieren. Diese wichtigen Messgrößen werden als Leistungskennzahlen (KPIs, Key Performance Indicators) bezeichnet. Ein KPI ist eine zählbare Messgröße, die von einem Unternehmen verwendet wird, um zu bestimmen, im welchem Ausmaß die operativen und strategischen Ziele erreicht werden. KPIs sind im Unternehmen eindeutig und basieren auf der Leistung jeder Abteilung, die für die Gewährleistung des Gesamtunternehmenserfolgs erwartet wird. Mehrere kombinierte Messgrößen können dabei einen einzelnen KPI bilden.
Zu den grundlegenden Merkmalen, die für die Einführung eines effektiven KPIs erforderlich sind, gehören:
- Einfach zu verstehen
- Messbar
- Istwert (aktuell)
- Geringe Anzahl
Quelle: „The Choice of KPIs in BSC implementation.“ Business Analysis Toolkit. 2008-2015. https://www.measurebusiness.com/the-choice-of-kpis-in-bsc-implementation.htm
Zweiter Schritt: Leistungskennzahlen definieren
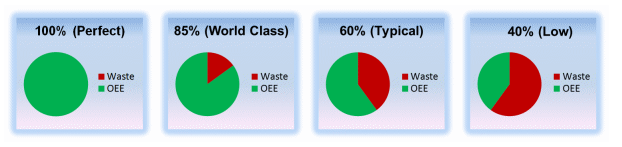
Abbildung 1: Erkennen der Bedeutung des GAE-Werts eines Unternehmens zur Erzielung von Verbesserungen und zur Identifikation von Problemen im Produktionsbereich.
Quelle: OEE (Overall Equipment Effectiveness). Vorne Industries, Inc. 2011-2016. https://www.leanproduction.com/oee.html
Als Folge des Auftretens von Ethernet in der Industrie und des damit verbundenen Wandels von eigenständigen Systemen zu einer vernetzten Anlage haben erstklassige Hersteller erkannt, dass sie die Produktivzeit der industriellen Netzwerkinfrastruktur als wichtigen Faktor der GAE berücksichtigen müssen. Auf Basis dieser Erkenntnis sucht das Management dieser Unternehmen nach Möglichkeiten, wie sie ihre Betriebsabläufe verändern können.
Viele Unternehmen haben zum Beispiel für die Netzwerkinfrastruktur der Fertigung eine Störungsbehebungsmentalität; wenn das Netzwerk also nicht verfügbar ist, muss dieses Problem sofort behoben werden, damit die Anlage wieder in Betrieb gehen kann. Dies ist eine direkte Folge der Verarbeitung von KPI-Daten für ein Anlagensegment (z. B. eine Maschine oder Zelle), die nicht notwendigerweise die vernetzte Natur des heutigen industriellen Betriebs widerspiegelt. Für Unternehmen, in denen sich Vorfälle im industriellen Netzwerk auf die Produktion auswirken, ist das eine entscheidende Vorgehensweise. Anstatt nach einer Unterbrechung in einer Zelle oder Maschine zu suchen, wenn die Auswirkungen klar ersichtlich sind, die ursprüngliche Ursache jedoch in Dunkeln liegt, wäre ein effektiverer Zugang möglicherweise die Untersuchung der Leistungsfähigkeit der gesamten Infrastruktur des industriellen Netzwerks und dessen Interaktionen mit den verschiedenen Maschinen in der Anlage.
Um einen KPI zu definieren, mit dessen Hilfe ein Unternehmen annähernd die idealen 100 % Netzwerkproduktivzeit erreicht, muss zuerst entschieden werden, welche Geräte innerhalb des Industrienetzwerks rund um die Uhr laufen müssen, etwa die Mensch-Maschine-Schnittstellen (MMS), Speicherprogrammierbare Steuerungen (PSPs), Eingabe/Ausgabe-Steuerungen (E/A), industrielle Schalter und Antriebe, die bei einem Defekt zum Ausfall der Produktion führen würden. Abbildung 2 zeigt die vielen Arten von Geräten, die Teil eines einzelnen industriellen Netzwerks sein können.
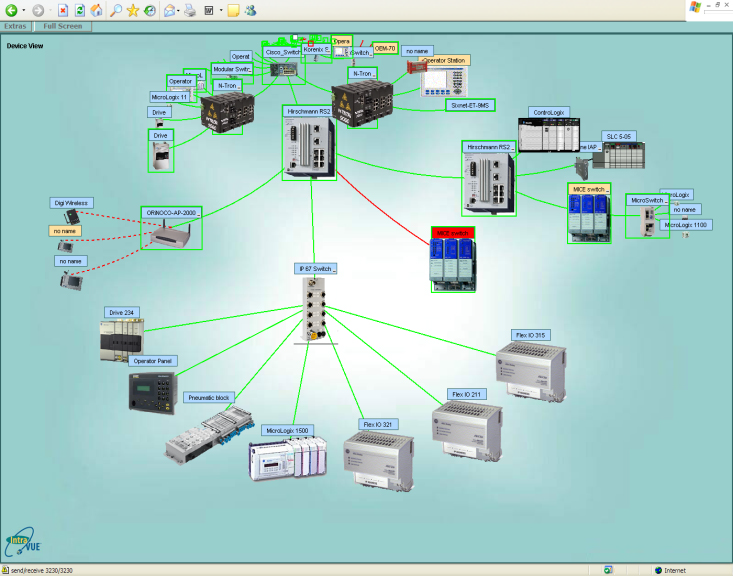
Abbildung 2: Dieses Schema zeigt die vielen Geräte und Anschlusspunkte, die Teil eines industriellen Netzwerks sein können.
Dritter Schritt: Fundierte Entscheidungen auf der Grundlage von KPI-Datenberichten treffen
Für jedes Unternehmen ist die Verfügbarkeit von Daten, auf deren Grundlage fundierte Entscheidungen getroffen werden können, von großer Bedeutung. Oftmals wird in einem Unternehmen die fortlaufende Verbesserung übersehen, weil es schwierig ist, Daten zur Verfügung zu stellen, aus denen die Vorteile von Verbesserungen gegenüber den Kosten ersichtlich sind. Für ein Fertigungsnetzwerk sind verfügbare Daten zur Bestimmung einer auftretenden Verschlechterung sowie von Bereichen, in denen Verbesserungen erforderlich sind, um das Netzwerk ordnungsgemäß zu verwalten und die Produktion der Anlage aufrecht zu erhalten, von entscheidender Bedeutung. So kann der Netzwerk-KPI zum Beispiel zeigen, dass die Anzahl von auftretenden Ereignissen im Netzwerk trotz einer Netzwerkverfügbarkeit oberhalb des angestrebten Wertes rasch ansteigt, was auf eine Netzwerkinstabilität hindeutet. Durch die Untersuchung dieser Daten kann möglicherweise eine zeitweilig unterbrochene Verbindung zu einem wichtigen E/A-Modul aufgezeigt werden, die erkannt und rasch behoben werden kann, bevor überhaupt ein Fehler auftritt.
Dank dieser Informationen kann das Kontroll- und Produktionsmanagement die Ausgaben für Kapitalinvestitionen rechtfertigen, die für vorbeugende Wartung erforderlich sind, anstatt sich auf einen reaktiven Wartungszugang zu stützen. Um die benötigten Daten zu erlangen, ist ein Werkzeug erforderlich, dass in der Lage ist, dem Kontroll- und Produktionsmanagement problemlos eine Momentaufnahme der Integrität des industriellen Netzwerks auf Basis von vordefinierten KPIs zu präsentieren. Das Kontroll- und Produktionsmanagement kann die KPIs mithilfe einer benutzerfreundlichen Web-Schnittstelle aus der Ferne überwachen. Werkzeuge wie die neue KPI-Berichtsfunktion in der Industrienetzwerk- und Visualisierungssoftware IntraVUE™ von Panduit® ermöglichen dem Management durch eine Visualisierung der Netzwerkleistung fundierte Entscheidungen auf Datenbasis (Abbildung 3).
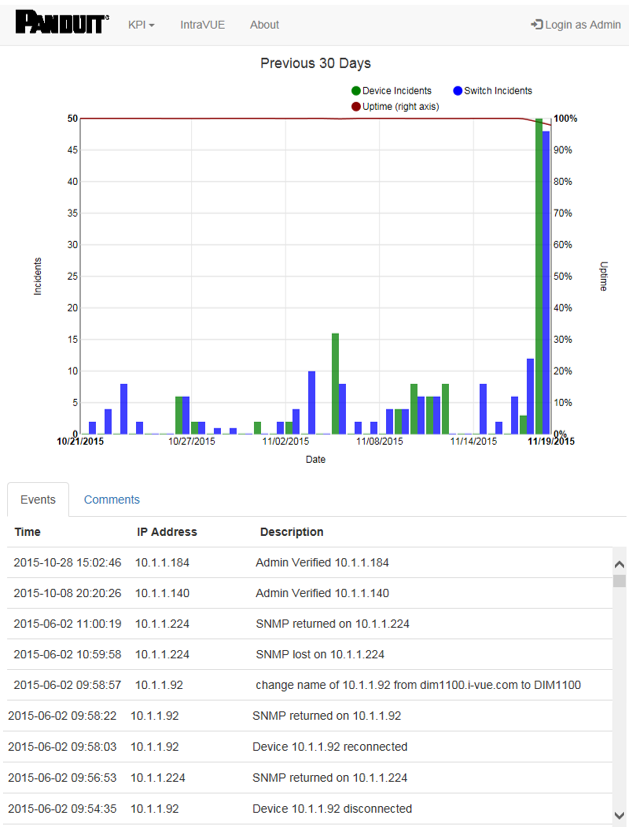